
List of All Welding Products

Vautid
VAUTID 80
For applications combining impact and abrasion
In VAUTID 80, finely distributed wear-resistant particles of chrome carbide form a reliable defense against abrasion wear. At the same time, their fine structure provides an elastic framework, thereby ensuring an extended service life under impact conditions.
VAUTID 80 is therefore ideal for parts which are exposed to a combination of impact and abrasion.
Among its applications, these properties have made VAUTID 80 the centerpiece of our wear protection system for the sugar industry.
Recommended applications:
Components which are exposed to temperatures up to 350°C.
Components subject to a combination of impact and abrasion
e.g. sieve bars and inlet funnel components.
Components which serve as impact elements or opposing bodies,
e.g. impactors and blades used in vegetation shredding equipment, impact mill housings, and components in recycling facilities.
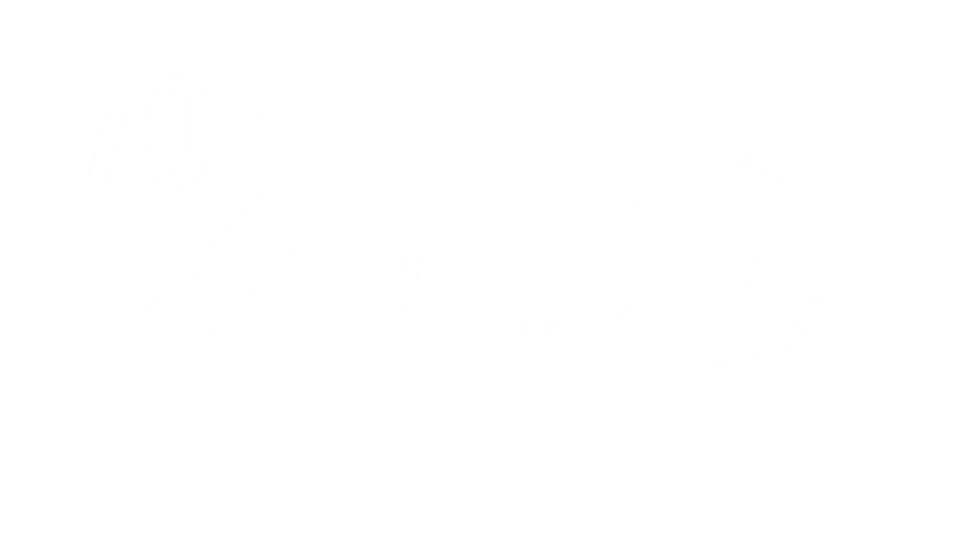
Vautid
VAUTID 70
For tough, hard, heat-resistant overlays in applications where there is a combination of impact and abrasion
The metal used in VAUTID 70 contains titanium, which forms one of the hardest types of carbide in existence. Because of its titanium carbide content, this alloy offers excellent resistance to abrasive wear. The carbides of titanium are embedded in an extremely tough matrix. This provides particularly effective protection against impact. Furthermore, weld layers constructed from VAUTID 70 are crack-free and resistant to high temperatures.
Hence VAUTID 70 offers ideal wear protection for components which operate at elevated temperatures and are simultaneously subject to high levels of abrasion and impact.
Recommended applications:
Components exposed to temperatures up to 670°C.
Components which are subject to significant impact from abrasive materials,
e.g. deflector plates, blast furnace throat armor, funnels and chutes.
Moving components which operate in highly abrasive media and either strike solid bodies at high speed or experience extreme pressures within the media, e.g. high-pressure rollers, parts of crusher rolls, roller presses and hammers in hammer mills.
Metal-on-metal wear applications, e.g. tools for hot forming or forging steel components.
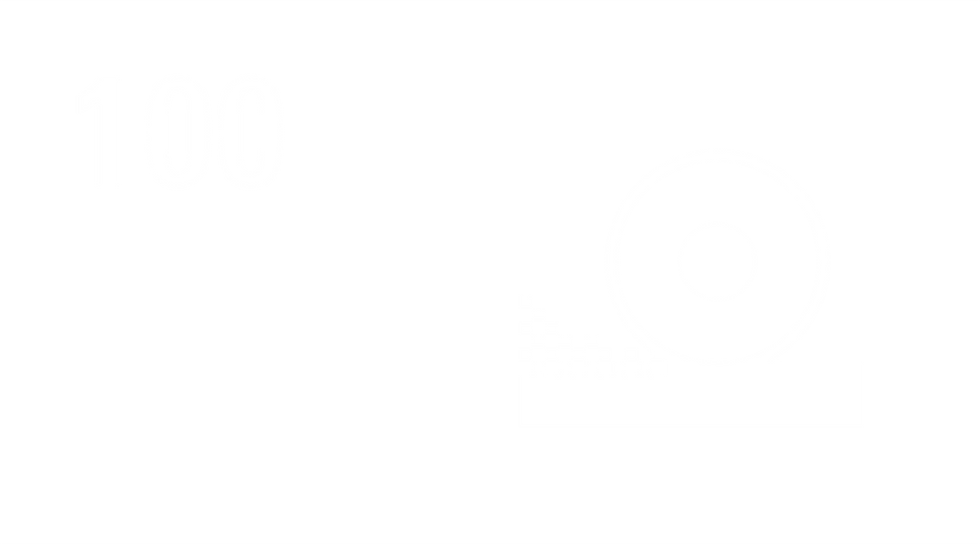
Vautid
VAUTID 100T
For wear-resistant hardfacing layers and wear-resistant hardfacing layers operating at raised temperatures
This member of the VAUTID 100 product family also embodies the extremely wear-resistant properties which are produced when chrome carbide is embedded within a stable matrix. Adding other alloying elements prevents the matrix from becoming destabilized by diffusion processes at temperatures over 350°C.
This raises the maximum operating temperature of VAUTID 100T to 550°C.
Recommended applications:
Components which are exposed to temperatures up to 550°C.
Components which carry a steady flow of abrasive media e.g. material slides, dust ducts, separators and ventilator fans.
Components that operate in homogenous, abrasive materials e.g. coking plant equipment, sinter crushers, clinker breakers, feeder screws and sieves.
This welding alloy is also available as a VAUTID composite wear plate, produced using a special metal arc welding process (VAUTID VVP 100T).

Vautid
VAUTID Ultra 304
A hardfacing welding consumable for exceptionally wear-resistant overlays, supplied as flux-cored wire
This welding consumable combines excellent abrasion resistance with the advantages of flux-cored wire. VAUTID Ultra 304 allows the user to produce, with a high degree of precision, an overlay of fused tungsten carbide in a matrix that retains its integrity when welded. This flux-cored wire features hard, non-melted particles of fused tungsten carbide, securely embedded within a wear-resistant iron-based matrix.
Hardness in position 1: 66 – 69 HRC (DIN 32525-4)
Recommended applications:
For a straightforward method of producing extremely wear-resistant layers using flux-cored wire.
For protecting filigree areas of components, e.g. edges and points.
Serial production parts which are subject to extreme wear and are produced on automatic welding machines, e.g. scraper bars, feeder screw edges, drill pipe guides, mixer paddles, and ploughshares.
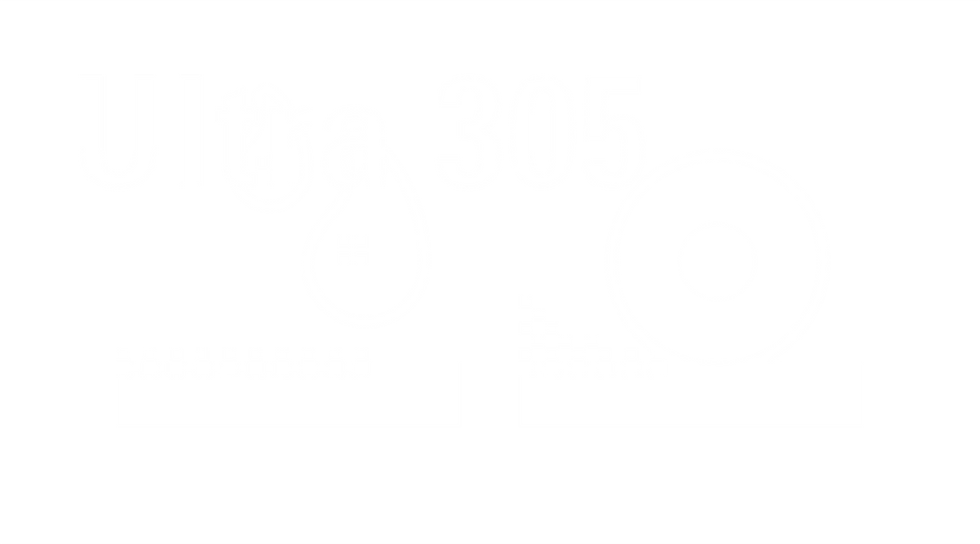
Vautid
VAUTID Ultra 305
A hardfacing welding consumable for exceptionally wear-resistant overlays, supplied as flux-cored wire
VAUTID Ultra 305 combines the exceptional wear resistance gained from using fused tungsten carbide (grain size 0.1 – 0.5 mm) with the ease of use of flux-cored wire . In addition, VAUTID Ultra 305 features an extremely tough nickel matrix, making it corrosion-resistant and capable of withstanding moderate impact without pitting.
Matrix hardness: ca. 550 – 650 HV10
Wear-resistant particles: ca. 2000 HV10
Recommended applications:
For a straightforward method of producing extremely abrasion-resistant and corrosion-resistant layers using flux-cored wire.
For protecting filigree areas of components, e.g. edges and points.
Serial production parts which are subject to extreme wear and corrosion and are produced on automatic welding machines, e.g. scraper bars, feeder screw edges, drill pipe guides, mixer paddles, and ploughshares.

Vautid
VAUTID Ultra 303
A hardfacing welding consumable in the form of a coated nickel wire, for producing overlays which are extremely abrasion-resistant and corrosion-resistant
As with the other products in the VAUTID Ultra family, fused tungsten carbide is used to deliver exceptional abrasion resistance in VAUTID Ultra 303. It also features a NiCrBSi matrix, which also ensures an exceptionally high level of corrosion resistance.
The standard grain size of the crushed fused tungsten particles, which are not bound to the matrix, is 0.3mm – 0.7mm. Where necessary, the formulation can be modified to a different grain size or to use a spheroidal form of fused tungsten carbide.
Matrix hardness: ca. 400 – 600 HV10
Tungsten carbide: ca. 2000 HV10 (DIN 32525-4)
Recommended applications:
Components which are subject to abrasion from corrosive media, e.g. water (including sea water), weathering, and diluted forms of caustic soda, phosphoric acid, formic acid and acetic acid.
Components which are subject to cavitation, or extreme wear arising from various classifications of contact (sliding, grooving, sliding particulate, or rolling particulate), e.g. sand preparation plants, excavator buckets, mixers, slurry pumps, feeder screws, grinding segments, mill hammers, soil augers, scraper blades, beater bars, and straightening machine guide rails.
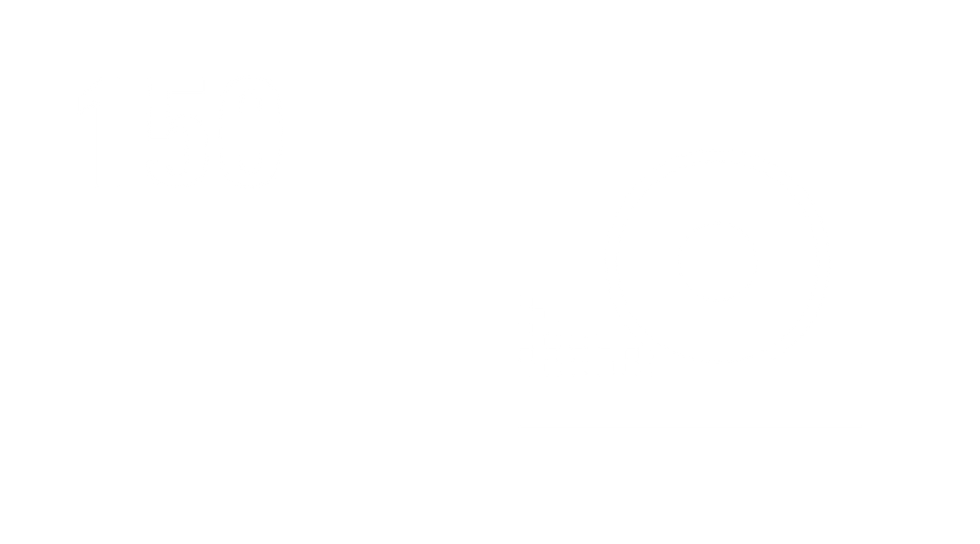
Vautid
VAUTID 150
For highly wear-resistant hardfacing in applications which also involve a low level of shock loading
Adding boron significantly increases the wear resistance of our classic VAUTID chrome carbide alloys. This is why VAUTID 150 produces a weld material with a particularly high hardness level. The boride and chrome carbide inclusions offer excellent resistance to abrasion.
Recommended applications:
Components which are exposed to temperatures up to 350°C.
Components which are subjected to significant abrasion combined with a low level of shock loading, e.g. compression screws and feeder screws, dust ducts, and separator and cyclone components.
This welding alloy is also available as a VAUTID composite wear plate, produced using a special metal arc welding process (VAUTID VVP 150).

Vautid
VAUTID 90
Palm oil industry
This material was designed to meet the specific wear conditions encountered in the palm oil industry.
Carbides of chrome are used to protect crushing mills against the effects of abrasive plant fibers. The carbides are dispersed extremely finely within the structure, giving this product the elasticity and plasticity to absorb the impacts and shocks that arise during operations.
Recommended applications:
Components which are exposed to temperatures up to 350°C.
Moving parts operating in abrasive media which encounter moderately hard objects, e.g. feeder screws in biomass applications.
Components which serve as impact elements or opposing bodies,
e.g. impactors and blades used in vegetation shredding equipment.

Vautid
VAUTID 100
The all-round solution for hardfacing layers with excellent wear resistance
VAUTID 100 is recognized around the world as the industry standard for wear protection. This well-proven specification forms the basis of the entire VAUTID 100 product family. The concept behind this overlay material is as follows: the right proportion of extremely wear-resistant hard particles embedded within a stable matrix.
This formulation offers an excellent price-to-performance ratio and covers a wide range of applications. In its basic form, VAUTID 100 is a great all-rounder. Its tried-and-tested characteristics have been modified for specific applications, leading to several variants: VAUTID 100 T, VAUTID 100 Mo and VAUTID 100 C.
Recommended applications:
Components which are exposed to temperatures up to 350°C.
Components which carry a steady flow of abrasive media e.g. material slides, dust ducts, separators, liners in mixing plants, and side wall surfaces and grinding tables in vertical mills.
Components that operate in homogenous, abrasive media e.g. excavator buckets, mixer buckets, feeder screws, wear liners, and separator bars in vertical mills.
This welding alloy is also available as a VAUTID composite wear plate, produced using a special metal arc welding process (VAUTID VVP 100).

Vautid
VAUTID 40
For impact loads and moderate abrasion
In impact load situations, it is important that the armored overlay is malleable and capable of being formed. This allows the kinetic energy of striking particles to be absorbed and, ideally, to be released again. VAUTID 40 meets this challenge in full. With its ductile matrix, this alloy offers exceptional protection against shock loadings, yet still contains a sufficient quantity of hard particles to provide moderate protection against abrasion as well.
It can even be machined after tempering, making this alloy particularly well-suited for the production of close-tolerance components. Very good results can also be achieved in metal-on-metal wear applications.
Recommended applications:
Components which are subject to both impact and abrasion, in applications where impact stresses are the major consideration, e.g. hammers for crushing plants handling moderately abrasive media.
Components which need to be machined after hard-facing.
Metal-on-metal wear applications, e.g. guides and rails.

Vautid
VAUTID 145
For hardfacing layers with an extremely high level of wear resistance and good heat resistance properties
Carbides of tungsten, niobium and vanadium are some of the hardest and most effective particles available for wear protection. They are all combined in our tried-and-tested VAUTID 145. This alloy offers reliable protection against both extreme abrasion and high temperatures.
Recommended applications:
Components which are exposed to temperatures of up to 750°C.
Components which are subjected to very high levels of abrasive wear
e.g. sinter crushers, glass recycling equipment, and the wear edges of excavator buckets and chain conveyors.
Components which are subjected to very high levels of abrasion at elevated temperatures, such as hot gas ventilation fans, hot dust ducts and blast furnace bell liners.
This welding alloy is also available as a VAUTID composite wear plate, produced using a special metal arc welding process (VAUTID VVP 145).
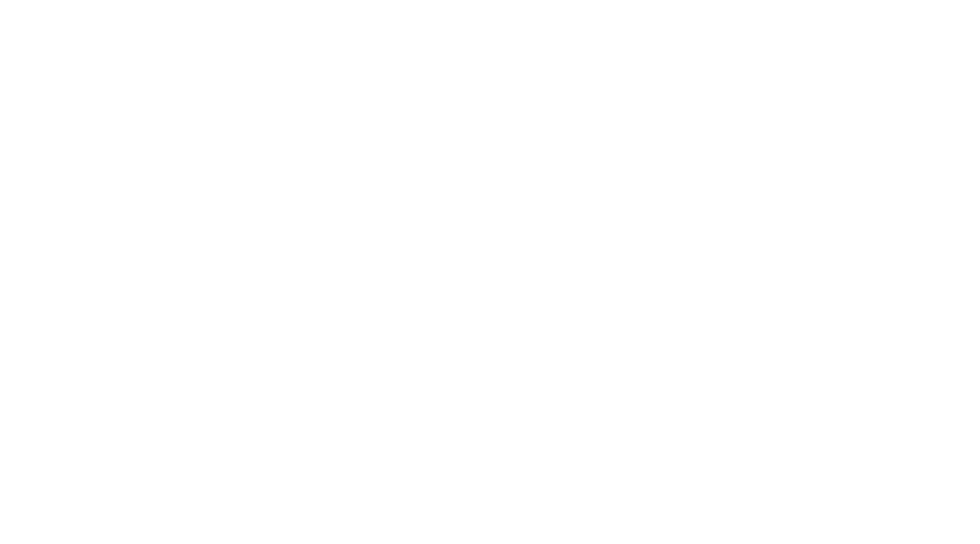
Vautid
VAUTID 60
For applications involving severe impact wear and for buffer layers
Shock loadings have a surface work-hardening effect on alloys with a high manganese content. With its very high manganese content, VAUTID 60 demonstrates exceptional resistance to impact wear.
This alloy produces an extremely tough, crack-resistant weld metal which is non-magnetic and has a high tensile strength. The material is characterized by excellent compatibility with all weldable steels, and it can be flame cut. Hence VAUTID 60 is suitable for tough, pressure-tight buffer layers and for hardfacing components which are predominantly subject to impact stresses. It is also suitable for the remanufacture of components made from high manganese steel, e.g. hammers, beater bars and crushing rolls.
Recommended applications:
Wear protection of components which are subject predominantly to impact stresses, e.g. impact heads, transfer points below fall pipes, and racks in blasting facilities.
As a buffer layer between components made of weldable steel and wear-resistant VAUTID welding consumables.
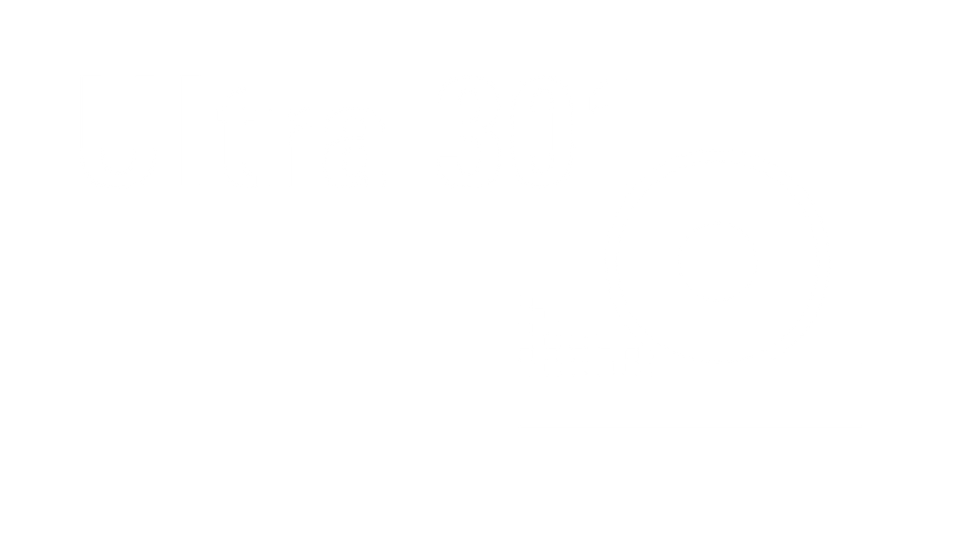
Vautid
VAUTID Ultra 301
A hardfacing welding consumable in the form of a filler rod for producing extremely wear-resistant hardfacing layers
In our VAUTID Ultra range, we use fused tungsten carbides to provide an exceptional level of wear resistance. VAUTID Ultra 301 weld metal comprises a steel matrix bonded with embedded particles of fused tungsten carbide (carbide grains sized 0.25 – 0.7 mm), in a combination which is free from any metallurgical contamination. The structure of the weld metal prevents the tungsten carbides from breaking out of the hard layer under the abrasion encountered in operation.
VAUTID Ultra 301 is usually welded with oxy-acetylene.
Matrix hardness: ca. 650 HV10
Tungsten carbide: ca. 2000 HV10 (DIN 32525-4)
Recommended applications:
Components subject to extreme abrasion, e.g. core bits, rolling cutter drill bits, deep hole boring bars, mixer paddles for extremely abrasive media, sand separators, ploughshares, clay pulverizing disks and scraper bars.
Particularly suitable for applying weld protection to edges.

Vautid
VAUTID 100C
For hardfacing layers with a high level of resistance to corrosion, heat and scaling
VAUTID 100C produces a welding product with a high level of resistance to corrosion, heat and scaling
It is non-magnetic and impact-resistant, and it can be cold formed. Overlays show minimal cracking, subject to the geometry of the component and the pre-heat temperature.
Recommended applications:
Components which are exposed to temperatures up to 350°C.
Comparable with cobalt-chrome materials.
Components which must have good abrasion resistance combined with good corrosion resistance and high impact strength, e.g. mixer and agitator components, and applications in the pulp and paper industries and the food processing sector.

Vautid
VAUTID 147
For hardfacing layers with an exceptionally high level of wear resistance and very good heat resistance properties
VAUTID 147 represents an improvement on our tried-and-tested VAUTID 145 specification.
The result is even greater protection against abrasive wear and an increase in maximum operating temperature. But, as always, we only use cost-effective wear absorption elements, enabling us to achieve the best possible price-performance ratio.
Recommended applications:
Components which are exposed to temperatures of up to 850°C.
Components which are subjected to very high levels of abrasive wear e.g. sinter crushers, glass recycling equipment, and material slides handling extremely abrasive media.
Components which are subjected to very high levels of abrasion at elevated temperatures, such as hot gas ventilation fans, hot dust ducts, blast furnace bell liners and screens in smelting plants.
This welding alloy is also available as a VAUTID composite wear plate, produced using a special metal arc welding process (VAUTID VVP 147).

Vautid
VAUTID 30
For pressure-tight, crack-resistant overlays and buffer layers
With its high compressive strength, this alloy is best suited for build-up layers and weld repairs to steel materials. This low-alloy welding consumable is crack-free, machinable and ductile.
Recommended applications:
As a buffer layer between steel components and wear-resistant VAUTID welding consumables.
When protecting or remanufacturing highly stressed machine components, such as crane pulleys, cable drums and rails.

Vautid
VAUTID 110
Best protection against combined impact and abrasion for horizontal and vertical welds (positions PC and PF)
This welding consumable produces a hardfaced layer that is both shock-resistant and impact-resistant. The metal flow characteristics have been designed for good weldability in positions PC and PF. This enables wear-resistant hardfaced layers to be produced on vertical surfaces. And that means plant improvement works can be carried out without the need for dismantling.
Recommended applications:
Producing layers which are both abrasion-resistant and impact-resistant in welding positions PC and PF.

Vautid
VAUTID 105
Best abrasion protection for horizontal and vertical welds (positions PC and PF)
With VAUTID high wear-resistance hardfacing welding consumables, the emphasis is on maximizing service life. Other properties, such as metal flow characteristics and the welding positions that these permit, are secondary to this overall objective.
However, if you need a wear-resistant welding consumable for special positions, then VAUTID 105 is the ideal choice. All VAUTID welding consumables are basically well suited to welding in positions PA and PB — but this alloy can also be used when welding in positions PC and PF.
Recommended applications:
For producing abrasion-resistant layers in welding positions PC and PF.

Vautid
VAUTID 50
For tough hardfacing layers in high shock load applications
Alloys with a high manganese content work harden under impact. Hence they are very well-suited to protect components which are subject to impact forces; because the more an area is impacted, the harder it becomes.
With VAUTID 50, any weldable component can acquire this useful attribute. This material is also equally suitable for remanufacturing components made from high manganese steel.
Recommended applications:
As a buffer layer between steel components and wear-resistant VAUTID welding consumables.
Components which are subject predominantly to impact stresses, e.g. impact heads, transfer points below fall pipes, and racks in blasting facilities.

Vautid
VAUTID 143
For highly wear-resistant hardfacing layers in applications with a combination of impact and abrasion
This material combines compact, needle-shaped chrome carbides with small, extremely hard niobium carbides. Because of their shape, niobium carbides serve to stabilize the wear-resistant weld overlay. They work like clamps, holding the structure together against impact-generated forces. At the same time, their extreme hardness increases abrasion wear resistance.
In VAUTID 143, chrome carbide and niobium carbide complement each other to produce a material which offers outstanding protection against both abrasion and impact.
Recommended applications:
Components which are exposed to temperatures up to 350°C.
Components which are exposed not only to severe abrasion but also to significant impact, e.g. funnels into which highly abrasive materials drop and slide.
Moving components which operate in highly abrasive media and strike solid bodies at high speed, e.g. roll liners in crusher mills and high-pressure finishing rollers.
Components which serve as impact elements or opposing bodies,
e.g. hammers in crushing mills processing hard materials, and beater bars.
This welding alloy is also available as a VAUTID composite wear plate, produced using a special metal arc welding process (VAUTID VVP 143).
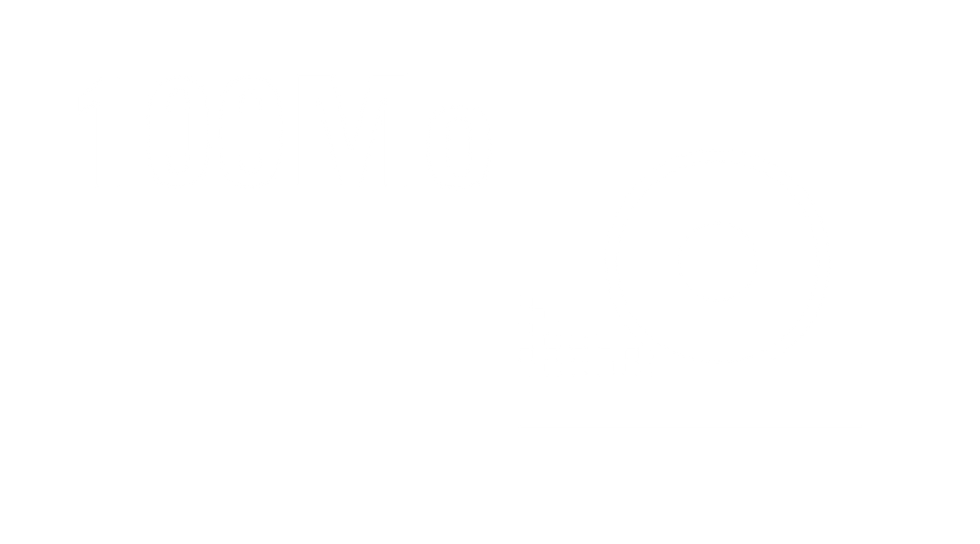
Vautid
VAUTID 100Mo
For highly wear-resistant hardfacing, even with a low level of impact
VAUTID 100Mo is a variant of our well-proven VAUTID 100 specification. In addition to carbides of chrome, this welding material incorporates finely distributed special carbides, which increase resistance against abrasion wear. In addition, because of a specific adjustment to the formulation, VAUTID 100Mo has a finer gain structure than VAUTID 100. As a result, this weld material responds more flexibly to shock loads. This improves wear resistance under light impact conditions.
VAUTID 100Mo is therefore best suited for overlays on components which are subjected to high levels of abrasion and moderate impact loads.
Recommended applications:
Components which are exposed to temperatures up to 350°C.
Components which carry a steady flow of abrasive media and are also subject to light impact, e.g. chutes and material slides onto which bulk material of a medium particle size falls and slides, and grinding tables in vertical mills where the material being milled contains even larger objects.
Moving components which operate in homogenous abrasive media and strike solid bodies at moderate speeds, e.g. rollers and wear liners operating in very homogenous materials where no foreign bodies are present in the mill stock, centrifugal separators for sand, excavator bucket teeth and bucket edge wear strips.

Vautid
VAUTID 18/8/6
For overlays and buffer layers subject to impact and pressure
This is a traditional material for weld joints and buffer layer applications. It ensures that VAUTID wear protection alloys fuse securely with austenitic manganese steel and hardening steels.
Due to its excellent corrosion resistance qualities, work-hardening capabilities and high ductility, VAUTID 18/8/6 is especially well-suited for the protection and remanufacture of components which are subject to impact and pressure loads.
Recommended applications:
Buffer layers between components made from austenitic manganese steel or hardening steels and wear-resistant VAUTID welding consumables.
For use when remanufacturing components which are made from austenitic manganese steel or which have a specific ductility or corrosion-resistance requirement, e.g. rails, railway points/shunting switches, firing bolts and gears.
Components subject to high temperatures used in mineral wool production.

Vautid
VAUTID 30/9
For buffer layers and hardfacing
Due to its high compressive strength, VAUTID 30/9 is the ideal product for build-up layers in weld repairs. As a buffer layer material, this alloy works not only with all weldable steels and weldable steel castings, but also — and equally well — with steels that are difficult to weld, such as Cr-Ni-Mo grades.
It is also extremely well suited as a buffer layer when joining VAUTID composite wear plates. This crack-resistant, rustproof welding metal has work-hardening properties and offers a high level of resistance to pressure, impact and cavitation.
Recommended applications:
As a buffer layer for components made from steels that are difficult to weld, such as Cr-Ni-Mo grades, and wear-resistant VAUTID welding consumables.
In the remanufacture of components which are made from steels that are difficult to weld or are specifically required to be rustproof.
To protect components that are subject to pressure, impact or cavitation.
To protect weld joints in fabrications made from VAUTID composite wear plates

Vautid
VAUTID Ultra 302
A hardfacing welding consumable in the form of an electrode rod for producing hardfacing layers with an exceptionally high level of wear resistance under low shock loading
VAUTID Ultra 302 comprises a wear-resistant iron-based matrix containing unfused particles of extremely hard tungsten carbide. The carbide grains (sized 0.25 – 0.7 mm) are securely confined within the matrix, which retains its integrity when welded. This product can be used to produce multiple layers (three layers maximum).
Matrix hardness: ca. 700 – 900 HV10
Tungsten carbide: ca. 2000 HV10 (DIN 32525-4)
Recommended applications:
Components subject to extreme abrasion, e.g. core bits, rolling cutter drill bits, deep hole boring bars, beater bars, ploughshares, grinding segments and scraper bars.
For producing tough hard surfaces from multiple layers.
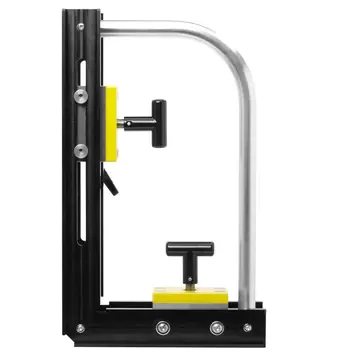
MagSwitch
90 Degree Angle 1000 - 8100503
Deliver superior accuracy with our fixed 90-degree welding angle. Adjust the MagSquares by sliding them up or down on each axis for unmatched versatility. Switch on and off 1052 pounds of magnetic holding force by rotating the black knobs. Comes ready to use with two MagSquares, as pictured.

MagSwitch
Magswitch Pivot Angle 200 - 8100367
Magswitch pivoting magnetic welding angle offers a range of angles from 28 degrees to 270 degrees. Switch on and off 215 pounds of magnetic holding force by rotating the black knobs. Two sides of the tool magnetize when turned on and can be secured to a table or wall to hold a fixture in place.

MagSwitch
Magswitch MagSquare 1000 - 8100099
The most versatile workholding and fixturing tool ever! Align and secure flat or round pieces of steel to fabricate angles. Pull corners, secure steel for cutting, use as a guide, make your own fixtures and more! Turn the knob on and off to control 1000 pounds of magnetic hold force.
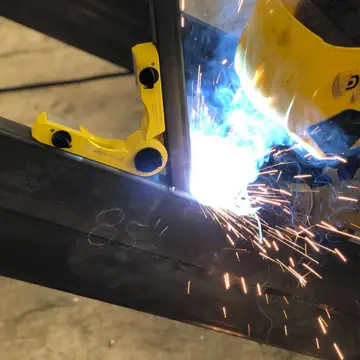
MagSwitch
Magswitch Pivot Angle 150 Max - 81001215
Magswitch Pivot Angle 150 Max has a holding angle range from 0 to 270 degrees, with each axis featuring a Magswitch magnet with a 150 lb. (68 kg) holding capability. No helping hands required. With interchangeable arms, this tool can be customized to fit in tight spaces! Arms compatible with Pivot Angle 150 Mini, sold separately. Get the job done by yourself with the Pivot Angle 150 Max workholding tool. Comes with a holster!
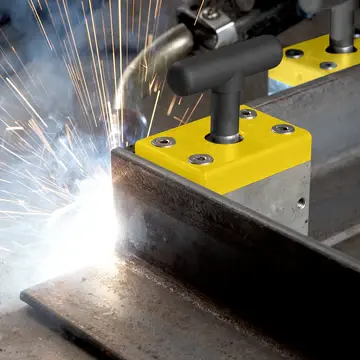
MagSwitch
Magswitch MagSquare 600- 8100106
The most versatile workholding and fixturing tool ever! Align and secure flat or round pieces of steel to fabricate angles. Pull corners, secure steel for cutting, use as a guide, make your own fixtures and more! Turn the knob on and off to control 607 pounds of magnetic hold force.

MagSwitch
MAGSWITCH Mini Tool Wall, Magnetic Tool Storage and Display Kit - 81001454
Store and display your Magswitch tools with the Mini Tool Wall. This bundle includes five tools: Ground Clamp (300 Amp), Multi Mini Angle, MagJig 150, MagMount 60 Keychain, and Magsquare 165. Each tool uses switchable magnets—just turn the knob for instant activation, no electricity required! Perfect for welding and fabrication.

MagSwitch
90 Degree Angle 165 - 8100548
Deliver superior accuracy with our fixed 90-degree welding angle. Adjust the MagSquares by sliding them up or down on each axis for unmatched versatility. Switch on and off 122 pounds of magnetic holding force by rotating the black knobs. Comes ready to use with two MagSquares, as pictured.

MagSwitch
Magswitch Pivot Angle 150 Mini - 81001269
Magswitch Pivot Angle 150 Mini has a holding angle range from 0 to 270 degrees, with each axis featuring a Magswitch magnet with a 150 lb. (68 kg) holding capability. No helping hands required. With interchangeable arms, this tool can be customized to fit in tight spaces! Arms compatible with Pivot Angle 150 Max, sold separately. Get the job done by yourself with the Pivot Angle 150 Max workholding tool. Comes with a holster!

MagSwitch
90 Degree Angle 600 - 8100495
Deliver superior accuracy with our fixed 90-degree welding angle. Adjust the MagSquares by sliding them up or down on each axis for unmatched versatility. Switch on and off 607 pounds of magnetic holding force by rotating the black knobs. Comes ready to use with two MagSquares, as pictured.
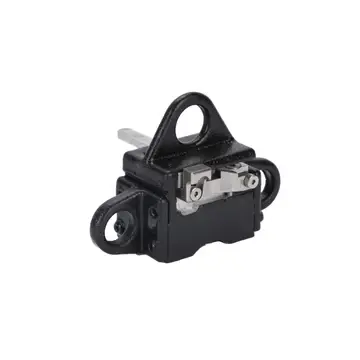
MagSwitch
Magswitch MagTether 300 - 8100111
Tether equipment or yourself while working above and below water. Turn the lever 180-degrees to switch on and off 247 pounds of magnetic hold force. The lever locks into place as a safety mechanism. The tether is sealed with a marine grade corrosion resistant coating to hold up to saltwater. Ideal for underwater welding, tethering, military and commercial oil and gas applications.

MagSwitch
Drill Press Vise Mount - 81001385
The Magswitch Drill Press Vise Mount makes it fast and easy to position and lock a drill press vise in place on a drill press table. The mount has four drop-in bolts that fit three T-slots positioned to accommodate a wide range of drill press vise mounting hole patterns. The drill press vise and mount can then be placed anywhere on a cast iron drill press table, and finely positioned until it is in place. Once in position, each of the 4 powerful switchable magnets locks the vise in place for the drilling operation.
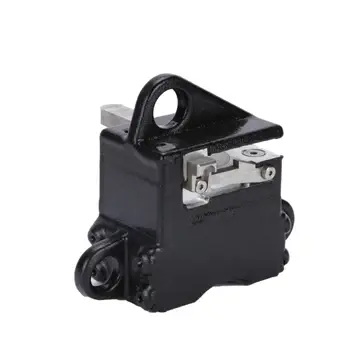
MagSwitch
Magswitch MagTether 1000 - 8100051
Tether equipment or yourself while working above and underwater. Turn the lever 180-degrees to switch on and off 1052 pounds of magnetic hold force. The lever locks into place as a safety mechanism. The tether is sealed with marine grade corrosion resistant coating to hold up to saltwater. Ideal for underwater welding, tethering, military, and commercial oil and gas applications.
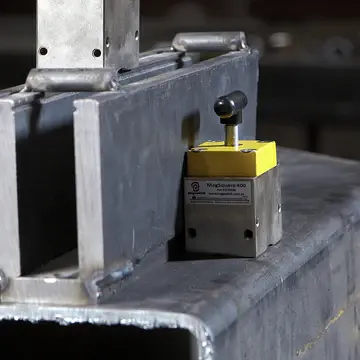
MagSwitch
MagSquare 400 - 8100238
The most versatile workholding and fixturing tool ever! Align and secure flat or round pieces of steel to fabricate angles. Pull corners, secure steel for cutting, use as a guide, make your own fixtures and more! Turn the knob on and off to control 399 pounds of magnetic hold force.
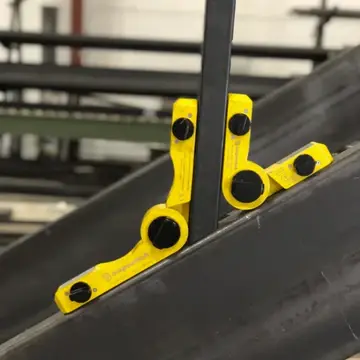
MagSwitch
Magswitch Pivot Angle 150 Bundle (Mini & Max) - 88001148
Magswitch Pivot Angle 150 Mini and Max each have a holding angle range from 0 to 270 degrees, with each axis featuring a Magswitch magnet with a 150 lb. (68 kg) holding capability. With interchangeable arms, this tool can be customized to fit in tight spaces. Get the job done safely and easily with our Pivot Angle 150 Series!

MagSwitch
Magswitch MagTether 600 - 8100077
Tether equipment or yourself while working above and underwater. Turn the lever 180-degrees to switch on and off 607 pounds of magnetic hold force. The lever locks into place as a safety mechanism. The tether is sealed with marine grade corrosion resistant coating to hold up to saltwater. Ideal for underwater welding, tethering, military, and commercial oil and gas applications.

MagSwitch
Magswitch MagSquare 165 - 8100494
The most versatile workholding and fixturing tool ever! Align and secure flat or round pieces of steel to fabricate angles. Pull corners, secure steel for cutting, use as a guide, make your own fixtures and more! Turn the knob on and off to control 150 pounds of magnetic holding force.

MagSwitch
Magswitch MagDrill Disruptor 55 - 81001155
The Magswitch MagDrill Disruptor 55 is a revolution in magnetic drilling technology. Smart Technology lets the magnets communicate with the 1600 W motor without the need for electricity. A perfect tool for welding, fabricating, heavy lifting, and infrastructure handling.
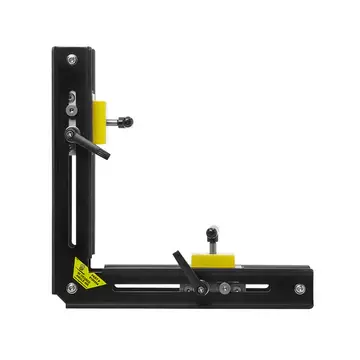
MagSwitch
90 Degree Angle 400 - 8100454
Deliver superior accuracy with our fixed 90-degree welding angle. Adjust the MagSquares by sliding them up or down on each axis for unmatched versatility. Switch on and off 400 pounds of magnetic holding force by rotating the black knobs. Comes ready to use with two MagSquares, as pictured.
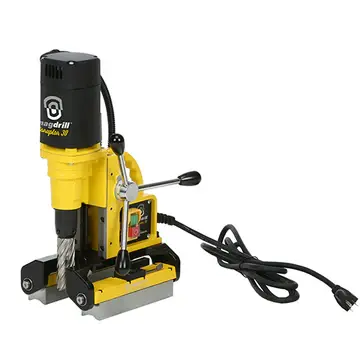
MagSwitch
Magswitch MagDrill Disruptor 30 - 8100920
The Magswitch MagDrill Disruptor 30 is a magnetic drill that utilizes patented shallow-field magnetic technology that offers incredibly strong grip on flat or curved surfaces, even on steel as thin as 1/8”. The base magnets swivel and automatically pivots to conform to any pipe 3” or larger.

MagSwitch
Magswitch MagSquare 165 UH - 8100610
The most versatile HIGH TEMP workholding and fixturing tool ever! Your favorite MagSquare that works at even higher temps. Align and secure flat or round pieces of steel to fabricate angles. Pull corners, secure steel for cutting, use as a guide, make your own fixtures and more! Turn the knob on and off to control 150 pounds of magnetic holding force.

Kemper
Welding Fume Extraction VacuFil 500
The high-vacuum suction and welding smoke extraction filter unit VacuFil 500 for high levels of smoke and dust is ideal for non-stop operation due to automatic filter cleaning. A side channel compressor to create negative pressure ensures robust performance for industrial users. In addition to up to four individual work station it can also be connected to a central pipe system.
.jpg)
Kemper
Welding Fume Cartridge Filter Unit Stationary
Due to its differential pressure-controlled, automatic filter cleaning system, the stationary cartridge filter for welding fume extraction is suitable for high levels of smoke and dust and non-stop operation with low operating costs. The KemTex® ePTFE membrane filter cartridges for ultra-fine dust particles separate particles even below 0.1 µm. The two-exhaust arm version with integral dampers allows simultaneous or alternating work in two places with adjustable extraction performance.

Kemper
WallMaster Welding Smoke Filter
The wall-mounted welding fume filtration system Wallmaster is a cost-effective filter solution for the modular setup of extraction systems. The filter medium integrated in a compact housing can be easily combined with both new and existing extraction elements. The SafeChangeFilter from KEMPER enables contamination-free filter changes, which also has a particularly high filter surface area of 42 square metres.

Kemper
Welding Smoke Exhaust Fan L
A universal, mobile solution for a variety of ventilation applications where filtering the air is not important. It is extremely quiet and is suitable for the extraction of e.g. welding fumes or car exhaust gases as well as for the fresh air ventilation of containers, pipes or manholes.

Kemper
ProfiMaster Welding Smoke Filter Unit
ProfiMaster is a robust smoke extraction filter unit for occasional to frequent use with low to medium amounts of dust. The high capacity disposable filter can easily be changed. The rotating and swiveling exhaust hood enables use in a 360-degree radius and ensures only few adjustments during welding.

Kemper
Welding Fume Extraction Unit WeldFil Compact
The solid yet compact welding smoke extraction system is ideally suited for factory buildings and welding shops with high levels of smoke and dust. Supplied ready to plug in and equipped with forklift pockets and lifting eyes, the WeldFil Compact is quickly installed as a central extraction and filter system for multiple welding work stations, cutting machines and welding robots. The KemTex® ePTFE membrane filter cartridges for ultra-fine dust particles separate particles even below 0.1 µm, and due to the W3/IFA Certification, the extraction filter unit WeldFil Compact is also suitable for use when machining chromium-nickel steel.
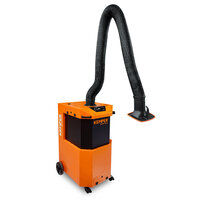
Kemper
MaxiFil Clean Welding Smoke Filter Unit
The welding smoke extraction unit MaxiFil Clean has a self-cleaning filter in combination with an automatic, contamination-freedust disposal. Its high mobility and a 360-degree operating radius make it the ideal device for continuous use. The simple filter unit easily handles applications with large amounts of smoke and dust.

Kemper
Welding Smoke Extraction VarioHood - Modular Extraction Hood
Due to its modular design the KEMPER variohood exhaust hood for welding robots can be configured in a number of sizes. Due to the innovative air flow principle, the hood requires only a low flow rate to operate effectively. Flexible set-up options, for instance mounting on stands in the room, suspended from the ceiling or integrated into a movable robot gantry, offer plenty of scope for plant design.

Kemper
Welding Fume Exhaust Arm 2 Joints
KEMPER exhaust arms unite high flexibility with ergonomic and safe workplace design. They can be used to extract welding smoke, gases and vapours as well as light dusts or solvents. With arms extending up to 6 meters, they are suitable for many different environments.
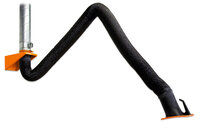
Kemper
Welding Smoke Exhaust Arm
The KEMPER air dust extraction arm is used for a single work station in conjunction with a fan or for multi-user stations using ducting connected to a central extraction and filter unit. The extraction arm is designed for continuous use and is suitable for high levels of fume, smoke and dust such as welding fumes, gases, vapours, light dusts or motor vehicle exhaust fumes.